
Just to hopefully summarise/expand the previous posts a little. I am in a meat processing facility goverened by the USDA.

I am wondering why we set critical and operational limits for metal detection within our HACCP plans if it is identified as a CCP, wouldn't we want to state that the critical limit is no metal? I am just slightly confused on this as we were asked if metal under those limits set is acceptable for a finished product. along this scenario, it will just be one day that they neglect the alarm and real contaminantion may happen. it will be hard for you to say in the HACCP plan my limit will be 1.2mm but during validation out of 200 good products it rejects around 60 good products that are without contaminant, then people may question the efficiency of metal detector and will be thinking "my equipment always reject even though it should not". this limit will be what you need to validate.Īs for to calibrate what is in the haccp plan,I think it is the other way around "at first".you validate your metal detector and the determined limit will be what you will have in the HACCP plan. in example they say the metal detector can detect up to 0.8mm SS however the scenario is it is only the one running among all machine with less traffic and movement to cause any signifcant vibration.if you do it real life production, there will be some interferences along your operation that make your metal detection limit be higher than 0.8mm already.

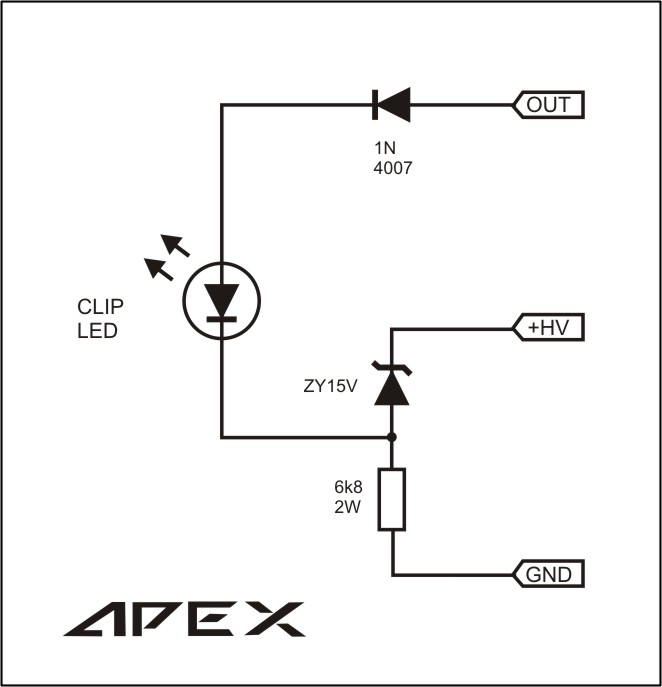
In case of MD and Xray the operational limit is at times the "best" condition for your MD to operate.
#Limits of a clipping detector verification
You need proof that the test bars function (detector is calibrated properly) and that the limits/sizes for the 3 different metals (stainless, ferrous and non ferrous) are based on sound science and/or regulatory standardsĪ) Validate.that means the metal detector WILL catch any pieces the same size as your test bars or greater under ALL working conditions (more than 1 piece of meat through the detector, piece on it's side so thicker than usual etc) WORST CASE SCENARIO-as long as nothing changes in the plant/type of meat/volume put through in a day this never needs done again.once/year you review the validation to make sure it matches what happens on a day to day basisī) Verify.during operations, the test bars are run through the detector to ensure it's functioning properlyĬ) equency of verification and by WHOM (don't forget to train them and make a record of the training)īTW-once you've got a meat plant under your belt, everything else will seem easy peasy!!! pardon the pun, but it's a great way to cut your teeth Sorry Elsa.VIC in Canada is Veterinarian In 's who gets to make the decisions on behalf of the USDA in the US
